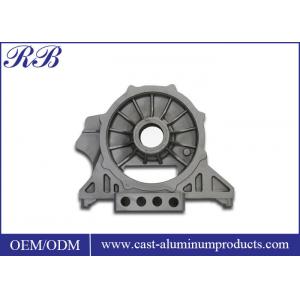
Add to Cart
ISO Certificated Foundry / High reliability Aluminum Alloy Castings
Product Description
Casting Process | Low pressure die casting |
Material | Cast Aluminum Alloy |
Surface Roughness | Ra3.2~0.4μm |
Dimension Tolerance | IT11-IT13 |
Payment Terms |
L/C, T/T |
Packaging Details | as per buyer requirement |
Delivery Time | 30 days |
Low Pressure Die Casting
Cold chamber die casting process
The cold chamber die casting process is very similar to the hot chamber die casting process. Molten metal is automatically or manually cast into the injection system by design that focuses on minimizing machine corrosion rather than production efficiency. This eliminates the necessity of immersing the injection mechanism in the molten metal bath.
For applications where the immersion design of hot chamber die castings is too corrosive, the cold chamber process may be a good choice. These applications include casting high melting point metals such as aluminum and aluminum alloys.
Precautions when choosing a die-cast alloy
The function and use of the final product will determine the choice of die casting alloy. For example, aluminum or copper based alloys may be an effective choice if the part requires high strength and corrosion resistance. Another consideration is production. With proper maintenance, aluminum die castings can last up to approximately 100,000 cycles, while zinc molds can last up to one million cycles before replacement. For long-term high volume production, it may be more cost effective to use alloys that maximize mold life.
Custom Product Process
Drawings, 3D files from customer →Technical review and quotation → Order confirmation → Mold design and making → Test and repairing mold → Making sample → Customer confirmation → casting → CNC machining → Surface treatment (optional) → Inspection → Packing → Delivery.
Payment terms & tooling lead time
--------Mould: 50% prepaid, balance will be paid after sample approval, normally tooling lead time is 30 days and sample lead time is 35 days, tooling lifetime is 50000shots.
--------Part: 50% before production, 50% after you receiving the copy of B/L, production lead time is about 30-45days.
MOQ
--------Each item is 100pcs/order, if quantity less than MOQ, set-up cost will be charged, one time trial production for small quantity after mold testing is ok.
Package
--------Standard packed in bubble bag then in carton, special request will be requoted
To receive accurate cost and time estimates for your custom casting project, please provide the following information of the parts you are requesting,
• Drawings(.dwg/.pdf)
• Material
• Quantity
• Quality acceptance criteria