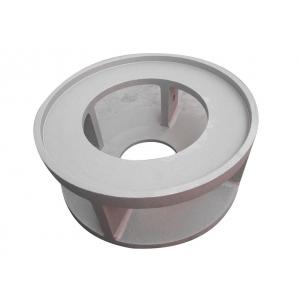
Add to Cart
Sand Aluminum Casting refers to a casting method for producing a casting in a sand mold.
Robot Arm Aluminum Casting is aluminum arm, Hydraulic and electric
Product Introduction
NOTICE:All the products on our website indicate the ranges we can manufacture and our production capability.
We offer cast aluminum products according to customer’s drawings or samples.
Please feel free to contact us if you have any questions or suggestions about our business.
Product Specification
Dimension Tolerance | CT8 |
Surface Roughness | Ra6.3-12 |
Manufacture | OEM/ODM |
Certificate | ISO9001:2015 |
Standard | ASTM, DIN,JIS, EN, ISO, GB |
Software | Pro/E,UG, Solidworks, Auto CAD, PDF |
Material | A356, A380, aluminum alloy or according to your requirements |
Machining | CNC turning, milling, drilling, grinding, cutting, reaming and threading |
Service | Sand casting, die casting, low pressure die casting, Gravity casting and CNC Machining |
Testing facility | Spectrometer, Tensile test machine, Hardness test machine, CMM (Coordinate Measuring Machine) |
Finished | Polishing, sand blasting, heat treatment, painting, powder coating, anodizing, electroplating, Chrome plating, mirror polishing. |
Product | All kinds of aluminum casting parts |
Quality Control
Casting Process
Packaging & Delivery
Our Customers
Office & Factory
Production Equipment
Additional Product Information
1) high casting efficiency. (85 ~ 95%)
Because there is no riser and gate, the gate is small, so the material cost and processing time can be greatly reduced.
2) perfect casting.
Easy to form directional solidification, less internal defects.
3) less involvement of gas and debris.
The pressure speed can be changed and the soup can be filled by laminar flow.
4) sand core can be used.
5) it is easy to realize automation and can operate multiple operations and processes.
6) not affected by the operator's proficiency.
7) wide use of materials.
8). Heat treatment can be carried out to enhance the performance.
Disadvantages:
1) the gate scheme has a small degree of freedom, which limits the product.
(restrictions on gate location and quantity, changes in product inner wall thickness, etc.)
2) long casting cycle and poor production.
In order to maintain directional solidification and fluidity, the mold temperature is high and the solidification speed is slow.
3) the structure near the gate is relatively thick, and the mechanical properties of the lower surface are not high.
4) comprehensive and strict management (temperature, pressure, etc.) is required.